Stöber
STÖBER
IOT APPLICATIONS FOR THE INDUSTRY
Thanks to these specially developed IoT applications, industrial machine drives can be parameterized and monitored.
Our story
01
The Challenge
We faced the challenge of parameterizing and monitoring industrial machine drives while synchronizing connected machines.
02
Our Solution
We implemented a real-time display of the controller and motor status, featuring intuitive navigation with customized UI/UX components. Our solution includes proprietary communication with the drive controller, enabling immediate display of parameter data changes. Additionally, we provide continuous monitoring and visual representation of critical states and events.
03
Successes
We achieved intuitive control of the machine drives and simplified the synchronization of connected machines. Additionally, we increased security through automated monitoring.
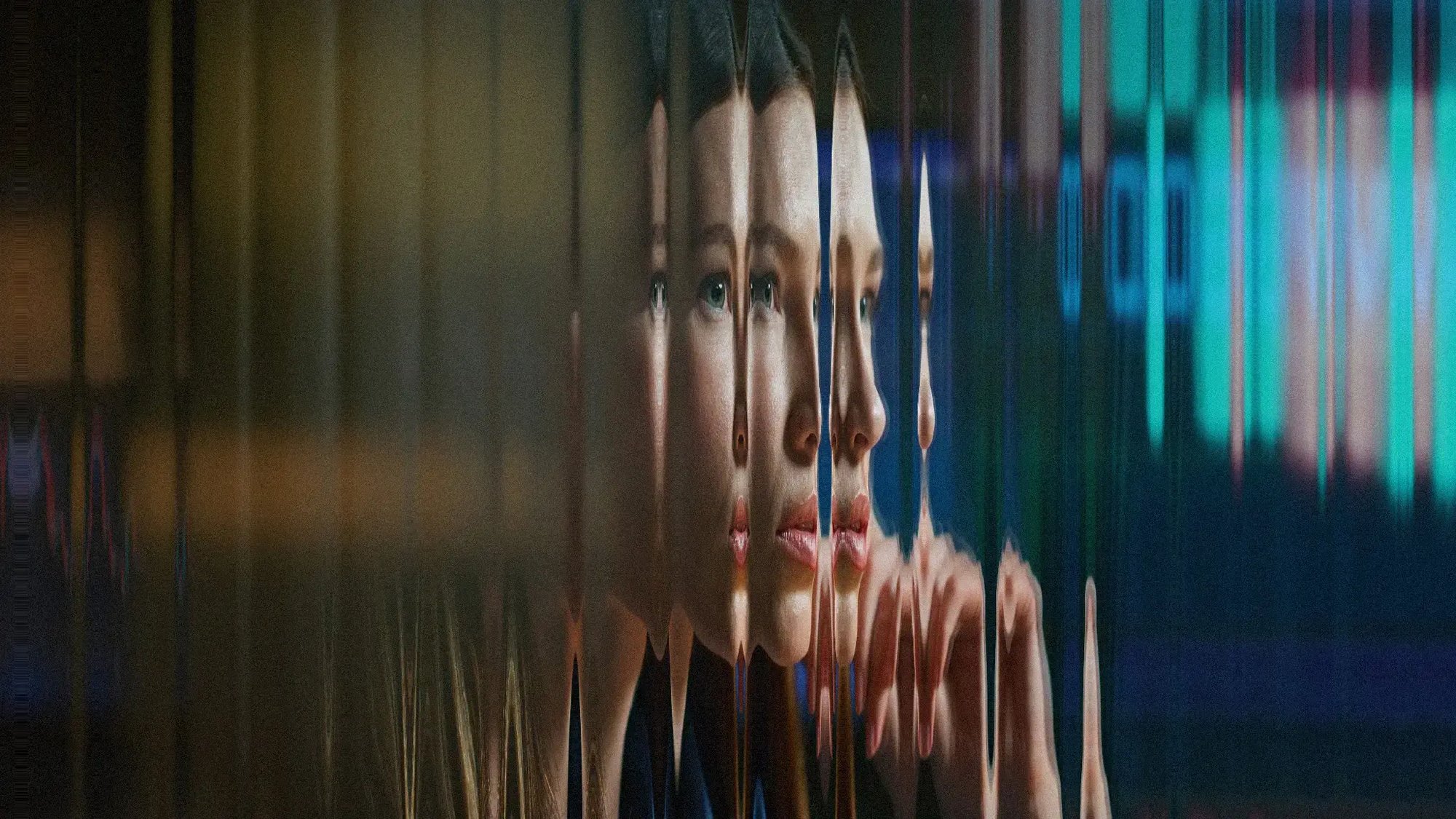
ABOUT STÖBER
Industry: Drive components
Business: B2B
Technology: Java, Redmine, Git, SVN
Web: www.stoeber.de
Stöber Antriebstechnik is a manufacturer and developer of drive components such as gear units, motors, drive controllers and device and user software. The family-run company from Germany operates worldwide and has branches in China, France, Great Britain, Italy, Japan, Austria, Switzerland, Taiwan, Turkey and the USA.
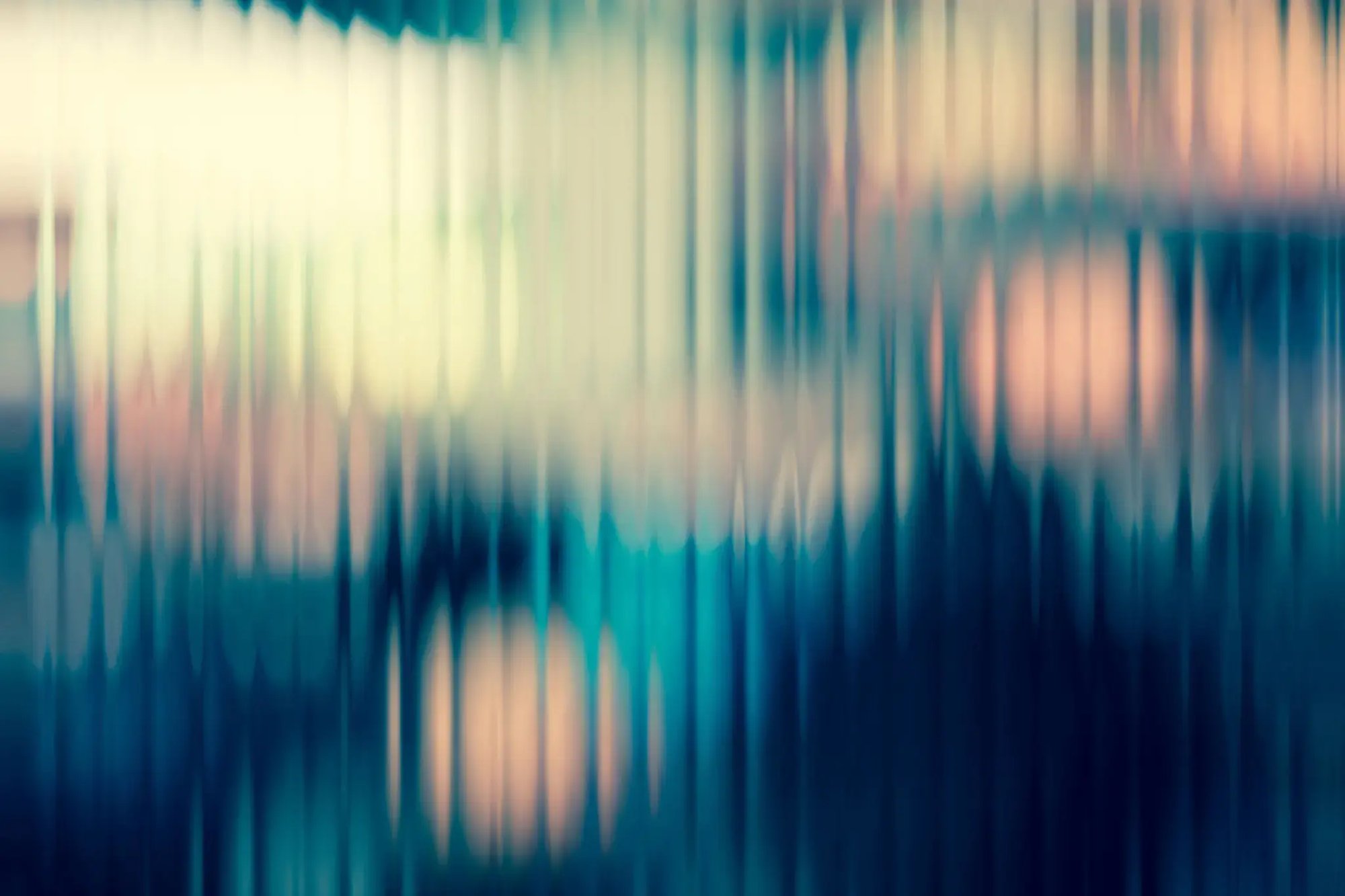
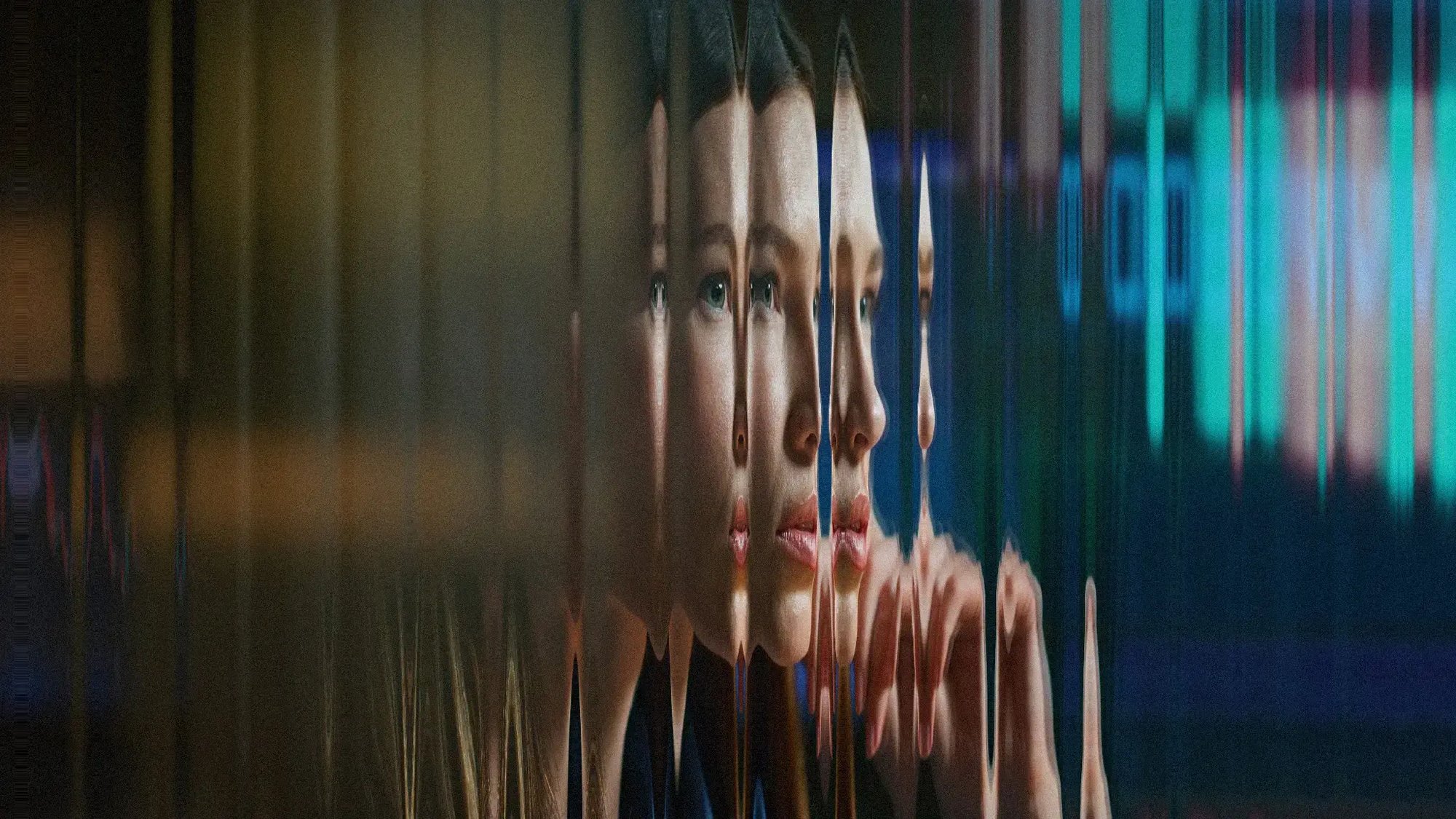
ready to update your business?
Let's talk!
Axel Wetten
senior business development manager
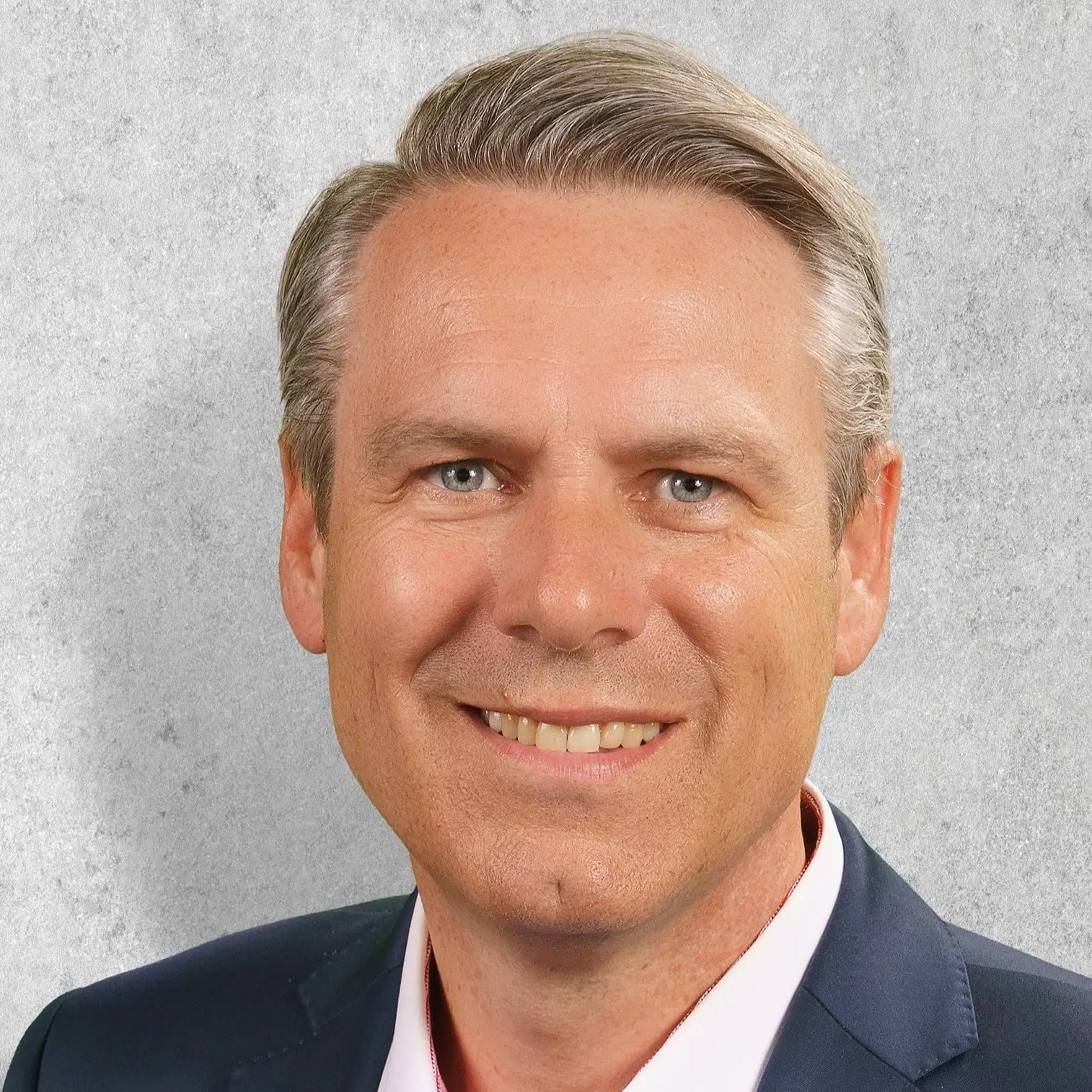
More success stories
Learn how we have empowered our customers and get to know our solutions
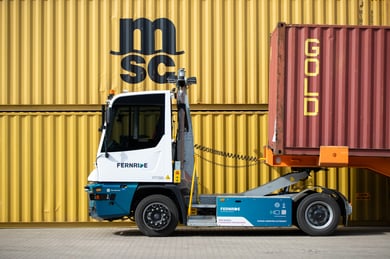
FERNRIDE
diconium performed comprehensive security testing for FERNRIDE to secure their autonomous vehicle systems against cyber threats.

Automotive
Connectivity Services: Increasing business value through optimized mobile applications

KiK
For our client KiK, we developed a high-performance e-commerce solution that stands out in the European market with its state-of-the-art architecture.

Medical aesthetics
We developed an innovative app for our client for the Apple Vision Pro VR headset, showcasing a medical product as an immersive 3D experience.

Industrial machinery manufacturer
Increasing sales efficiency and improving the customer experience through Salesforce solutions: For our client, we implemented an AI-powered solution that optimizes the sales process, reducing order processing time by 40% and speeding up proposal preparation by over 25%. Additionally, customer interactions were improved, onboarding was simplified, and data-driven decision-making was enabled.
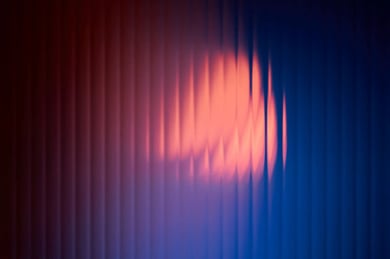
Automotive manufacturer
With a state-of-the-art, customer-centric data collection and analysis process, diconium integrates information into a new central dashboard—enabling valuable insights for the entire organization to capture and evaluate customer-centric touchpoints across multiple platforms and markets.